Rund 90 Millionen Euro plant die Treibacher Industrie AG in eine neue Recyclinganlage für Katalysatoren aus der Erdölindustrie zu investieren, weitere zehn Millionen Euro in den Neubau eines Logistikzentrums unmittelbar anschließend an das Werksgelände in Althofen. Am 28. und 29. Oktober werden dazu die mündlichen Behördenverhandlungen nach dem Abfallwirtschaftsgesetz (AWG) im Kulturhaus von Althofen durchgeführt, Umweltverträglichkeitsprüfung muss keine durchgeführt werden.
Die Vorstände der Treibacher Industrie AG (TIAG), Rainer Schmidtmayer und René Haberl, sind "guter Dinge", das Genehmigungsverfahren erfolgreich zu absolvieren. Seit eineinhalb Jahren werden Unterlagen und Gutachten für die größte Einzelinvestition der vergangenen 20 Jahre vorbereitet. Ziel ist eine Inbetriebnahme der neuen Anlage Mitte 2023. Dann wird auch die bestehende Recyclinganlage aus den Jahren 1978/1979, in der seit 20 Jahren Katalysatoren der Ölindustrie wiederverwertet werden, abgestellt.
Worum geht es dabei eigentlich genau?
Schwere Rohöle, insbesondere aus Russland und dem Karibischen Becken, enthalten die Metalle Vanadium, Nickel und einen hohen Anteil an Schwefel – solche Rohöle werden in bestimmten Raffinerien in Europa in Spezialanlagen mithilfe von chemischen Katalysatoren zu hochwertigen Ölen bzw. Zwischenprodukten verarbeitet.
Unter "Katalysatoren" versteht man wenige Millimeter große Partikeln in Kugel- oder Würstchenform. Sie lösen einen chemischen Prozess aus – im konkreten Fall reichern sie sich etwa um die Metalle Vanadium und Nickel sowie Schwefel an, und werden dann aus dem Prozess ausgestoßen. Die verbrauchten Katalysatoren, welche die Metalle Molybdän, Vanadium, Nickel, Schwefel und Öl enthalten, gelten dann als gefährlicher Abfall, der aufbereitet werden kann.
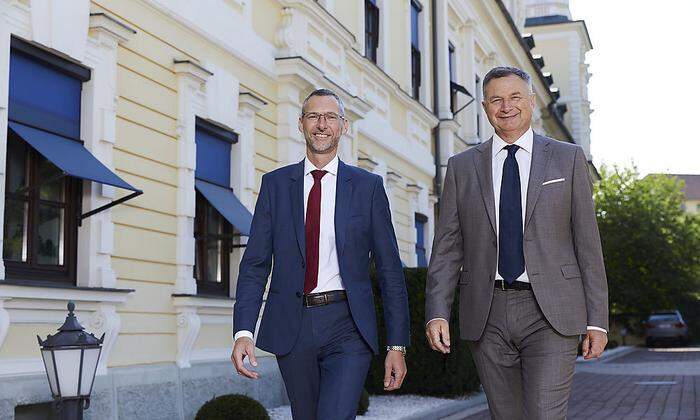
Und hier kommt die Treibacher ins Spiel. In Treibach werden über 90 Prozent der Katalysatoren – in Summe werden rund 20.000 Tonnen aufbereitet – zu Wertstoffen verarbeitet. Die Kapazität der neuen Anlage soll um rund zehn Prozent wachsen. Damit will man künftig 20 Prozent des europäischen Vanadium-Marktes bedienen – ein Metall, das auf der EU-Liste der kritischen Rohstoffe steht.
Die ölhaltigen Katalysatoren werden dabei unter geringem Energieaufwand (wofür derzeit Erdöl verwendet wird und künftig Erdgas) "geröstet". Dabei entsteht Abwärme, die von anderen Betrieben der TIAG genutzt wird, und schwefelhaltiges Rauchgas, das über eine Reinigungsanlage geführt wird und als Nebenprodukt Calciumsulfat ergibt – ein Düngemittel. In einem zweiten metallurgischen Schritt wird der geröstete Katalysator unter Zugabe etwa von Aluminium und Kalk zu Vanadium, Nickel und Molybdän, und diese in der Folge zu Ferrolegierungen verarbeitet, die an die Stahlindustrie geliefert bzw. nach Nordamerika, China und Korea exportiert werden. Der daraus erzeugte Stahl wird etwa für Werkzeuge, Autos und zum Bau von Hochhäusern verwendet.
66 Millionen Euro pro Jahr
Mit dem ertragsmäßig hochattraktiven Prozess setzen die Treibacher pro Jahr 66 Millionen Euro um – rund zehn Prozent des Konzernumsatzes. Das Geschäftsmodell sei, erklärt Schmidtmayer, zukunftssicher: "Wenn die Metallpreise hoch sind, zahlen wir der Raffinerie für die Abnahme Geld, sind sie niedrig, erhalten wir Geld." Bereits heute ist die TIAG mit einem Anteil von 70 Prozent Marktführer in Europa.
Der Kreislaufprozess, der ein Beitrag zum Green Deal der EU sein soll, erspare den Abbau von jährlich 500.000 Tonnen Erz, das entspricht 25.000 Lkw-Ladungen, betont Vorstand Haberl. Schwefel und Dampf, die beim Prozess entstehen, werden intern verwertet. Was bleibt, sind rund 200 Tonnen an Reststoffen, die deponiert werden müssen – der Anteil verwendbaren Wertstoffe soll mit dem Neubau der Anlage weiter auf 99 Prozent steigen. Obwohl es "deutliche Verbesserungen" geben werde, rechnen die Vorstände mit möglichen Widerständen gegen das Projekt, wenngleich ihnen noch keine Bürgerinitiative bekannt ist. Aus Gründen der Transparenz lade man die Bevölkerung am Freitag, 18. September, von 14 bis 18 Uhr zu einer Covid-konformen Informationsmesse in die Werkskantine.
