So leicht es geht. Und dennoch stabil genug, um einen rasenden Zug sicher auf Schiene zu halten. Es ist ein schmaler Grat, auf den sich das Forscherteam rund um die Maschinenfabrik Liezen und Gießerei (MFL) mit seinen Federtöpfen begibt. Diese vergleichsweise kleinen Teile sind in Drehgestellen von Hochgeschwindigkeitszügen verbaut, gelten als sogenannte "Hochsicherheitsteile". Das Team hat es nach intensiver Forschung geschafft, die Federtöpfe um mehr als ein Fünftel leichter zu machen, von 62 auf 49 Kilogramm. Jetzt stehen sie kurz vor der Serienproduktion.
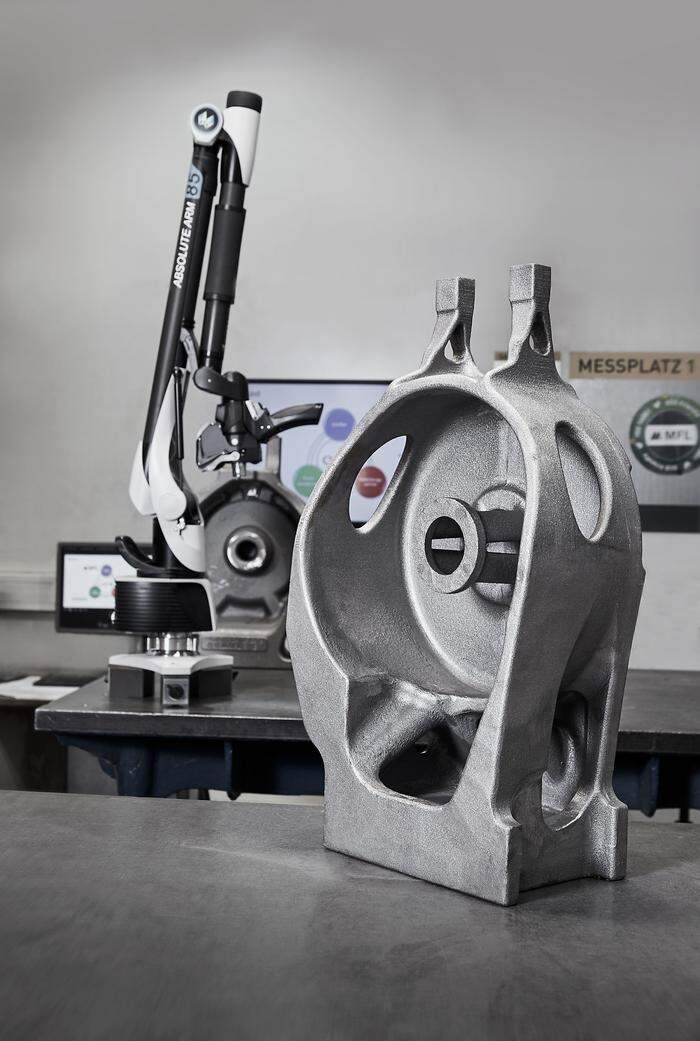
Warum das Gewicht der Teile eine so große Rolle spielt? Das zeigt sich allein schon bei der Produktion, erklärt Herbert Decker, Geschäftsführer von MFL: "Wir sparen Material, wir sparen Energie und CO₂-Emissionen." Im Ausmaß von 15 Prozent, das wurde im Rahmen des Projekts berechnet. Und auch der Zug fährt klimafreundlicher, weil er insgesamt weniger wiegt und dadurch weniger Energie verbraucht. Dazu kommt, dass die Schienen nicht so stark verschleißen.
Leicht, aber belastbar
Zurück zur Gratwanderung des Forscherteams: "Es ist darum gegangen, die Geometrie und die Wandstärken der Federtöpfe so weit zu reduzieren, dass man auf ein minimales Gewicht kommt, aber das Bauteil die Belastung noch aushält, wenn der Zug fährt", schildert Decker.
MFL leitet das Projekt, mehrere Forschungseinrichtungen sind beteiligt. Zusammen wurde mithilfe von Simulationen getüftelt: Welche Kräfte wirken wann auf das Bauteil? Wo sind die Schwachstellen, wo darf kein Material entnommen werden und wo geht das problemlos? Schlussendlich kam ein 3D-Drucker zum Einsatz, um einen Federkopf-Prototyp herzustellen. Bald sollen die Teile im großen Stil gefertigt werden.
"Transportmedium der Zukunft"
Auf den Schienenverkehr hat sich das Liezener Unternehmen schon länger spezialisiert. "Das ist das Transportmedium der Zukunft", betont Decker. Mittlerweile kann man als Unternehmen sowohl Einzelteile als auch schienenfertige Fahrzeuge liefern.
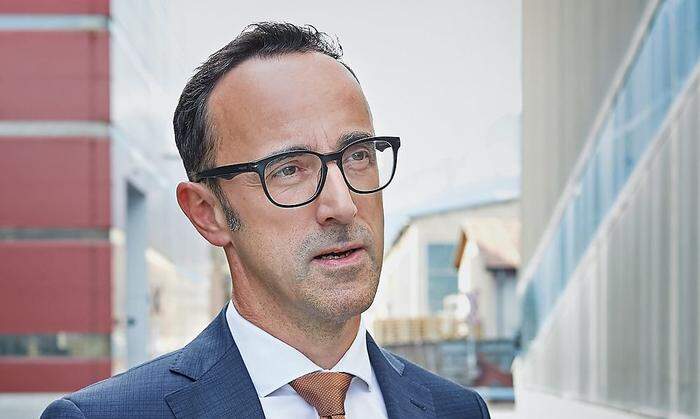
Der Fokus liegt auf "innovativen Wagen" für jene Güter, die in irgendeiner Art und Weise einen besonderen Transport benötigen. Denn: "Wir müssen noch viel mehr Güter auf die Schiene bringen, um die Klimaziele zu erreichen", sagt Decker. Und das mit nachhaltigen Bauteilen wie den Federtöpfen ist der Geschäftsführer überzeugt.
Klimakonferenz in Ägypten
Allgemein achte man als Unternehmen darauf, Ressourcen zu schonen. Das will man demnächst bei der UN-Klimakonferenz in Ägypten beweisen. Dort wurde MFL als eines von weltweit 50 Unternehmen eingeladen, um das eigene Nachhaltigkeitsprogramm zu präsentieren. "Wir werden auch diskutieren, wie wir die Industrie in die Richtung bringen können, dass wir nicht Teil des Problems, sondern der Lösung sind."
Seit 2012 hat MFL ein "zertifiziertes Energiemanagement" laufen. Im Jahr 2018 hat man bei den Wärmebehandlungsöfen in der Gießerei Anlagen dazu installiert, um Wärme zurückzugewinnen. Das große Ziel: Bis 2030 um ein Drittel weniger Energie verbrauchen.
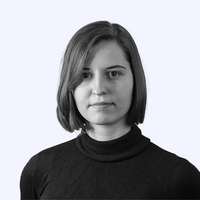