Dem Laien mag es einerlei erscheinen: Ob Metall schweißen, drücken oder tiefziehen – unterscheidet sich das Ergebnis am Ende? Radkersburger Metal Forming (rm) weiß, dass der Unterschied wesentlich ist. Und das nutzt das Unternehmen mit seinen 100 Mitarbeitern und Sitz in Radkersburg zu seinem Vorteil.
"Es ist unser Alleinstellungsmerkmal, dass wir komplexe Geometrien aus einem Stück fertigen, ganz ohne Schweißnaht. Wir können zwar auch schweißen, vermeiden es aber", erklärt Christina Merlini, Prokuristin des Unternehmens. Man hat sich auf die sogenannte nahtlose Metallumformung spezialisiert. Was das genau bedeutet?
Wie und warum nahtlos umformen?
Das Endprodukt wird nicht aus mehreren Stücken zusammengeschweißt, sondern aus einem einzigen Metallstück geformt. Die Techniken, die angewendet werden, sind etwa das Tiefziehen und das Drücken des Materials. "Aufgrund der von uns entwickelten Technologien können wir die Techniken kombinieren. Wir können Teile zum Beispiel vor-drücken und mit dem Ziehen fertigstellen", erklärt Entwicklungsleiter Boris Recek.
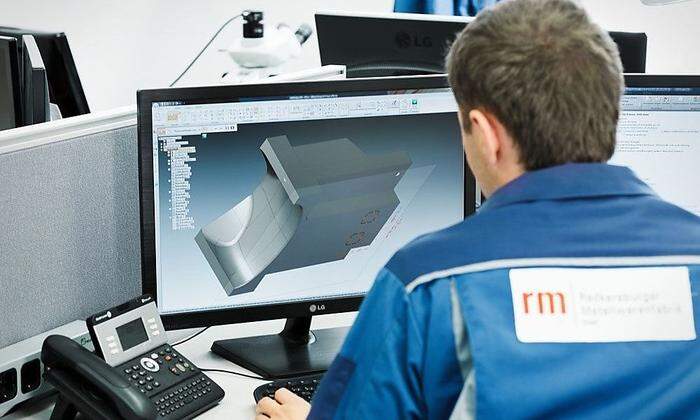
Die Frage nach dem "Wie" dürfte demnach beantwortet sein, aber "Warum" nahtlos umformen? "Das Resultat sind stabilere Teile. Jede Schweißnaht ist eine Schwachstelle und kann zu Rissen führen. Schweißen ist immer auch ein Kostenthema", meint Recek. Die nahtlose Umformung sei billiger, außerdem würde man an Gewicht sparen und Bakterien würden sich aufgrund der fehlenden Nahtstellen weniger schnell bilden.
Weltweit einzigartige Luftfederkolben und ein besonders leichter Lawinenairbag
Von der Skizze bis zum fertigen Produkt erarbeitet das Team von "rm" gemeinsam mit seinen Kunden Lösungen. Die Metallteile sind besonders in der Premium-Klasse der Autoindustrie gefragt. Etwa entwickelte das Unternehmen einen Luftfederkolben mit weltweit einzigartigem Drei-Kammern-Luftsystem für das Stoßdämpfersystem eines Autos. "Durch das Weg- oder Zuschalten der Kammern ist der Fahrstil des Autos wählbar: Fahre ich lieber in der sportlichen oder der Komfort-Fahrweise?", erklärt Merlini. Weil die nahtlose Umformung auch im Designbereich aufgrund der makellosen Oberfläche der Teile gefragt ist, werden beispielsweise auch Abdeckungen für Lautsprecher in Sportwägen produziert.
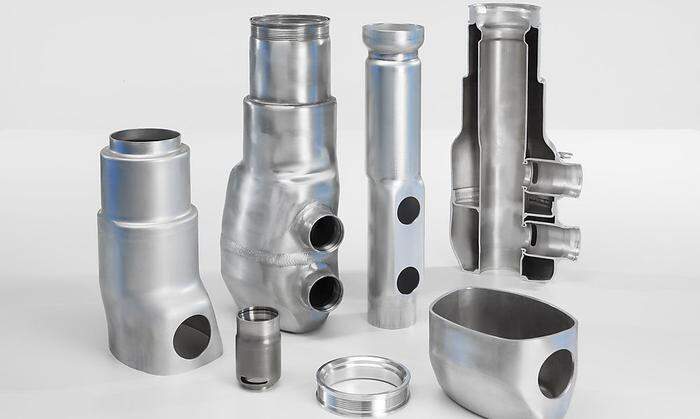
Neben der Automobilindustrie arbeitet das Unternehmen auf 7000 Quadratmetern Fläche im Radkersburger Gewerbepark für die Medizin- und Energietechnik oder die Lebensmittelindustrie. Kürzlich wurde ein Druckspeicher für Lawinenairbags entwickelt: "Der besteht ebenfalls aus nur einem Teil. Wir sind europaweit die Einzigen, die das machen. Für den Airbag ist das von Vorteil, weil der Druckspeicher sehr leicht ist", so Entwicklungsleiter Boris Recek.
Trotz Corona mit "Technologien überzeugen"
Derzeit könnte die Auftragslage des Unternehmens coronabedingt besser sein. Besonders in der Automobilindustrie hätten sich Aufträge, die einmal dringend waren, auf unbestimmte Zeit nach hinten verschoben. Klein beigeben will das Unternehmen aber nicht, im Gegenteil: "Wir sind ständig dran neue Innovationen zu entwickeln und unsere Prozesse zu verbessern. Wir wollen mit unseren Technologien überzeugen", so Recek.
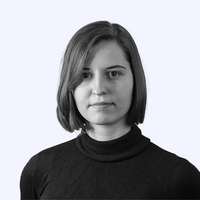